فناوری ذوب
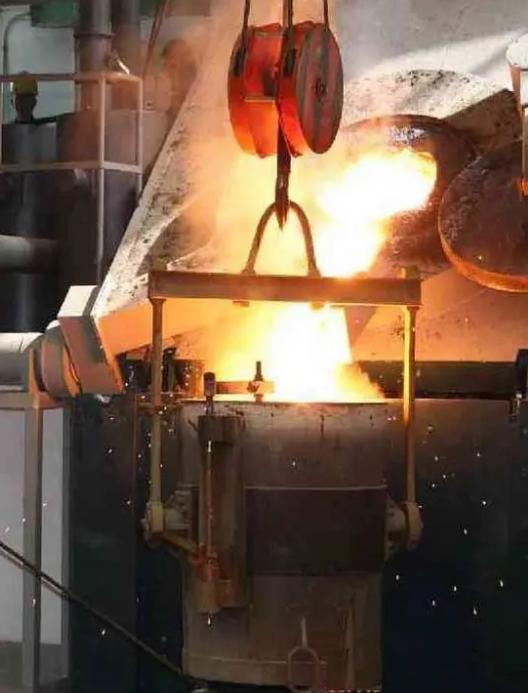
در حال حاضر، ذوب محصولات پردازش مس به طور کلی کوره ذوب القایی را اتخاذ می کند، و همچنین ذوب کوره طنین دار و ذوب کوره شفت را اتخاذ می کند.
ذوب کوره القایی برای انواع مس و آلیاژهای مس مناسب است و ویژگی ذوب تمیز و تضمین کیفیت مذاب را دارد. با توجه به ساختار کوره، کوره های القایی به کوره های القایی هسته ای و کوره های القایی بدون هسته تقسیم می شوند. کوره القایی هسته دار دارای ویژگی های راندمان تولید بالا و راندمان حرارتی بالا است و برای ذوب مداوم انواع مس و آلیاژهای مس مانند مس قرمز و برنج مناسب است. کوره القایی بدون هسته دارای ویژگی های سرعت گرمایش سریع و جایگزینی آسان انواع آلیاژی است. برای ذوب مس و آلیاژهای مس با نقطه ذوب بالا و انواع مختلف مانند برنز و مس نیکل مناسب است.
کوره القایی خلاء یک کوره القایی مجهز به سیستم خلاء مناسب برای ذوب مس و آلیاژهای مسی است که به راحتی استنشاق و اکسید می شوند مانند مس بدون اکسیژن، برنز بریلیم، برنز زیرکونیوم، برنز منیزیم و غیره برای خلاء الکتریکی.
ذوب کوره طنین دار می تواند ناخالصی ها را از مذاب تصفیه و حذف کند و عمدتاً در ذوب ضایعات مس استفاده می شود. کوره شفت نوعی کوره ذوب پیوسته سریع است که دارای مزایای بازده حرارتی بالا، سرعت ذوب بالا و خاموش شدن راحت کوره است. قابل کنترل است؛ هیچ فرآیند پالایشی وجود ندارد، بنابراین اکثریت قریب به اتفاق مواد خام مورد نیاز است که مس کاتدی باشد. کوره های شفتی معمولاً با ماشین های ریخته گری پیوسته برای ریخته گری پیوسته استفاده می شوند و همچنین می توان از کوره های نگهدارنده برای ریخته گری نیمه پیوسته استفاده کرد.
روند توسعه فناوری تولید ذوب مس عمدتاً در کاهش تلفات ناشی از سوختن مواد خام، کاهش اکسیداسیون و استنشاق مذاب، بهبود کیفیت مذاب و اتخاذ راندمان بالا منعکس شده است (نرخ ذوب کوره القایی بیشتر است. بیش از 10 تن در ساعت)، در مقیاس بزرگ (ظرفیت کوره القایی می تواند بیشتر از 35 تن در مجموعه باشد)، عمر طولانی (عمر پوشش 1 تا 2 سال است) و صرفه جویی در انرژی (مصرف انرژی القایی). کوره کمتر از 360 کیلووات ساعت در تن است)، کوره نگهدارنده مجهز به دستگاه گاززدایی (گاز زدایی CO) است، و کوره القایی سنسور ساختار اسپری را اتخاذ می کند، تجهیزات کنترل الکتریکی از تریستور دو طرفه به علاوه منبع تغذیه تبدیل فرکانس استفاده می کند. پیش گرم کردن کوره، وضعیت کوره و سیستم نظارت و هشدار میدان دمای نسوز، کوره نگهدارنده مجهز به دستگاه توزین است و کنترل دما دقیق تر است.
تجهیزات تولید - خط برش
تولید خط برش نوار مسی یک خط تولید برش و برش پیوسته است که کلاف عریض را از طریق کویل باز می کند و سیم پیچ را از طریق دستگاه برش به عرض مورد نیاز برش می دهد و از طریق سیم پیچ آن را به چند سیم پیچ برمی گرداند.(Storage Rack) از جرثقیل برای نگهداری رول ها روی قفسه ذخیره سازی استفاده کنید
↓
(ماشین بارگیری) از چرخ دستی تغذیه استفاده کنید تا رول مواد را به صورت دستی روی درام کویلر قرار دهید و آن را سفت کنید.
↓
(لوله کش و غلتک فشار ضد شل شدن) سیم پیچ را با کمک راهنمای بازشو و غلتک فشار باز کنید.
↓
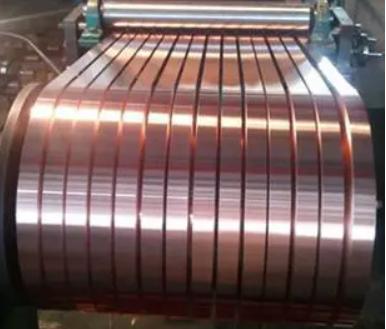
(NO·1 looper and Swing Bridge) ذخیره سازی و بافر
↓
(دستگاه غلتک راهنمای لبه و پینچ) غلتک های عمودی ورق را به غلتک های پینچ هدایت می کنند تا از انحراف جلوگیری شود، عرض غلتک راهنمای عمودی و موقعیت آن قابل تنظیم است.
↓
(دستگاه برش) برای موقعیت یابی و برش وارد دستگاه برش شوید
↓
(تغییر سریع صندلی چرخشی) تعویض گروه ابزار
↓
(دستگاه سیم پیچ قراضه) ضایعات را برش دهید
↓ (میز راهنمای انتهای خروجی و درپوش دم سیم پیچ) لوپر NO.2 را معرفی کنید
↓
(پل نوسانی و حلقه NO.2) ذخیره سازی مواد و حذف اختلاف ضخامت
↓
(دستگاه جداسازی شفت کشش صفحه فشار و هوا) نیروی کششی، صفحه و جداسازی تسمه را فراهم می کند.
↓
(برشی برش، دستگاه اندازه گیری طول فرمان و میز راهنما) اندازه گیری طول، قطعه بندی سیم پیچ با طول ثابت، راهنمای نخ نواری
↓
(سیم پیچ، دستگاه جداسازی، دستگاه فشار صفحه) نوار جداکننده، کلاف
↓
(کامیون تخلیه، بسته بندی) نوار مسی تخلیه و بسته بندی
فناوری نورد گرم
نورد گرم عمدتاً برای نورد بیلت شمش برای تولید ورق، نوار و فویل استفاده می شود.
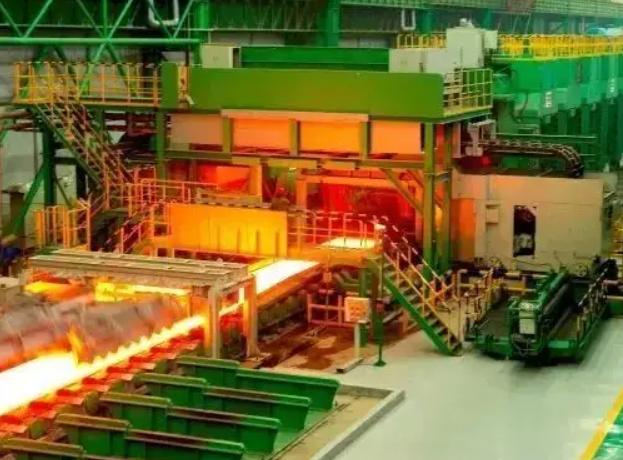
مشخصات شمش برای نورد بیلت باید فاکتورهایی مانند تنوع محصول، مقیاس تولید، روش ریختهگری و غیره را در نظر بگیرد و به شرایط تجهیزات نورد (مانند دهانه رول، قطر رول، فشار نورد مجاز، قدرت موتور و طول میز غلتکی) مربوط میشود. و غیره به طور کلی، نسبت بین ضخامت شمش و قطر رول 1: (3.5 ~ 7): عرض معمولا برابر یا چند برابر عرض محصول نهایی است و عرض و مقدار پیرایش باید به درستی باشد. در نظر گرفته شده است. به طور کلی عرض دال باید 80 درصد طول بدنه رول باشد. طول شمش باید با توجه به شرایط تولید به طور منطقی در نظر گرفته شود. به طور کلی، با این فرض که دمای نورد نهایی نورد گرم را می توان کنترل کرد، هرچه شمش طولانی تر باشد، راندمان و بازده تولید بالاتر می رود.
مشخصات شمش کارخانه های فرآوری مس کوچک و متوسط معمولاً (60 ~ 150) میلی متر × (220 ~ 450) میلی متر × (2000 ~ 3200) میلی متر است و وزن شمش 1.5 ~ 3 تن است. مشخصات شمش کارخانه های بزرگ فرآوری مس به طور کلی (150 تا 250) میلی متر× (630 تا 1250) میلی متر× (2400 تا 8000) میلی متر است و وزن شمش 4.5 تا 20 تن است.
در حین نورد گرم، دمای سطح رول در لحظه ای که رول با قطعه نورد با دمای بالا در تماس است، به شدت افزایش می یابد. انبساط حرارتی مکرر و انقباض سرد باعث ایجاد ترک و ترک در سطح رول می شود. بنابراین در هنگام نورد گرم باید خنک کاری و روانکاری انجام شود. معمولاً از آب یا امولسیون با غلظت کمتر به عنوان محیط خنک کننده و روان کننده استفاده می شود. نرخ کل کار نورد گرم به طور کلی 90٪ تا 95٪ است. ضخامت نوار نورد گرم به طور کلی 9 تا 16 میلی متر است. آسیاب سطحی نوار پس از نورد گرم می تواند لایه های اکسید سطحی، نفوذهای رسوبی و سایر عیوب سطحی ایجاد شده در هنگام ریخته گری، گرمایش و نورد گرم را حذف کند. با توجه به شدت عیوب سطحی نوار نورد گرم و نیاز فرآیند، میزان آسیاب هر طرف 0.25 تا 0.5 میلی متر است.
کارخانه های نورد گرم عموماً کارخانه های نورد معکوس با دو یا چهار ارتفاع هستند. با بزرگ شدن شمش و طولانی شدن مداوم طول نوار، سطح کنترل و عملکرد آسیاب نورد گرم روند بهبود و بهبود مستمر دارد، مانند استفاده از کنترل اتوماتیک ضخامت، رول های خمشی هیدرولیک، جلو و عقب. رول های عمودی، فقط رول های خنک کننده بدون خنک کننده دستگاه رولینگ، رول TP (Taper Pis-ton Roll) تاج کنترل، کوئنچ آنلاین (کوئنچ) پس از نورد، کویلینگ آنلاین و سایر فناوری ها برای بهبود یکنواختی ساختار نوار و خواص و به دست آوردن بهتر بشقاب
فناوری ریخته گری
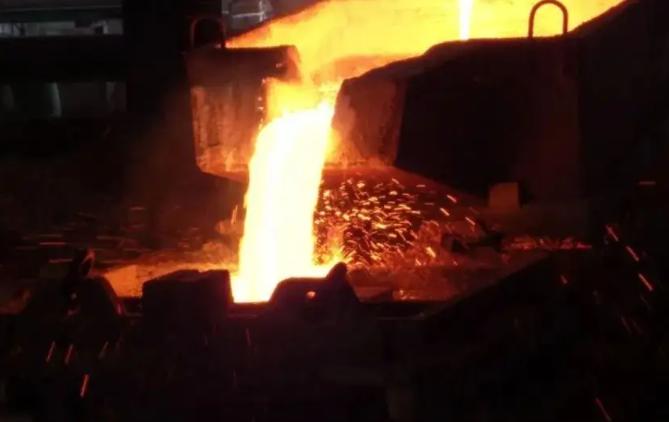
ریخته گری مس و آلیاژهای مس به طور کلی به دو دسته تقسیم می شود: ریخته گری نیمه پیوسته عمودی، ریخته گری پیوسته عمودی، ریخته گری پیوسته افقی، ریخته گری پیوسته رو به بالا و سایر فناوری های ریخته گری.
الف. ریخته گری نیمه پیوسته عمودی
ریخته گری نیمه پیوسته عمودی دارای ویژگی های تجهیزات ساده و تولید انعطاف پذیر بوده و برای ریخته گری انواع شمش های گرد و مسطح مس و آلیاژهای مس مناسب است. حالت انتقال دستگاه ریخته گری نیمه پیوسته عمودی به هیدرولیک، پیچ سربی و سیم طناب تقسیم می شود. از آنجایی که گیربکس هیدرولیک نسبتاً پایدار است، بیشتر مورد استفاده قرار گرفته است. کریستالایزر را می توان در صورت نیاز با دامنه ها و فرکانس های مختلف ارتعاش کرد. در حال حاضر روش ریختهگری نیمه پیوسته در تولید شمشهای مس و آلیاژ مس کاربرد فراوانی دارد.
ب. ریخته گری کامل و مستمر عمودی
ریختهگری پیوسته عمودی دارای ویژگیهای خروجی زیاد و بازده بالا (حدود 98%)، مناسب برای تولید شمش در مقیاس بزرگ و مداوم با تنوع و مشخصات واحد است و در حال تبدیل شدن به یکی از روشهای اصلی انتخاب برای ذوب و ریختهگری است. فرآیند در خطوط مدرن تولید نوار مسی در مقیاس بزرگ. قالب ریخته گری کامل و پیوسته عمودی از کنترل خودکار سطح مایع لیزری غیر تماسی استفاده می کند. دستگاه ریخته گری عموماً از بستن هیدرولیک، انتقال مکانیکی، اره کردن براده خشک با روغن خنک شده آنلاین و جمع آوری تراشه، علامت گذاری خودکار و کج کردن شمش استفاده می کند. ساختار پیچیده است و درجه اتوماسیون بالا است.
ج. ریخته گری پیوسته افقی
ریخته گری پیوسته افقی می تواند بیلت و بیلت سیمی تولید کند.
ریخته گری پیوسته افقی نواری می تواند نوارهای مس و آلیاژ مس را با ضخامت 14-20 میلی متر تولید کند. نوارها در این محدوده ضخامت را می توان مستقیماً بدون نورد گرم نورد سرد کرد، بنابراین اغلب برای تولید آلیاژهایی استفاده می شود که نورد گرم آنها دشوار است (مانند قلع، برنز فسفر، برنج سرب و غیره)، همچنین می توانند برنج تولید کنند. کوپرونیکل و نوار آلیاژ مس کم آلیاژ. بسته به عرض نوار ریخته گری، ریخته گری پیوسته افقی می تواند 1 تا 4 نوار را به طور همزمان ریخته شود. ماشینهای ریختهگری پیوسته افقی که معمولاً مورد استفاده قرار میگیرند، میتوانند همزمان دو نوار، هر کدام با عرض کمتر از 450 میلیمتر، یا یک نوار با عرض نوار 650-900 میلیمتر ریختهگری کنند. نوار ریختهگری پیوسته افقی معمولاً فرآیند ریختهگری فشار معکوس کشش را انجام میدهد و خطوط کریستالیزاسیون دورهای روی سطح وجود دارد که معمولاً باید با آسیاب از بین بروند. نمونه های داخلی از نوارهای مسی با سطح بالا وجود دارد که می توان آنها را با کشیدن و ریخته گری بیلت های نواری بدون فرز تولید کرد.
ریخته گری پیوسته افقی بیلت های لوله، میله ای و سیمی می تواند 1 تا 20 شمش را به طور همزمان با توجه به آلیاژها و مشخصات مختلف ریخته شود. به طور کلی، قطر میله یا سیم بلانک 6 تا 400 میلی متر و قطر بیرونی لوله خالی 25 تا 300 میلی متر است. ضخامت دیواره 5-50 میلی متر و طول جانبی شمش 20-300 میلی متر است. مزایای روش ریخته گری پیوسته افقی این است که فرآیند کوتاه است، هزینه ساخت کم است و راندمان تولید بالا است. در عین حال، این یک روش تولید ضروری برای برخی از مواد آلیاژی با کارایی گرم ضعیف است. اخیراً این روش اصلی برای ساخت بیلت از محصولات مسی رایج مانند نوارهای برنز قلع فسفر، نوارهای آلیاژ روی نیکل و لولههای تهویه مطبوع مس بدون اکسید فسفر است. روش های تولید
معایب روش تولید ریختهگری پیوسته افقی عبارتند از: انواع آلیاژی مناسب نسبتاً ساده، مصرف مواد گرافیتی در آستین داخلی قالب نسبتاً زیاد است و ساختار کریستالی سطح مقطع شمش یکنواخت نیست. آسان برای کنترل قسمت پایینی شمش به دلیل اثر گرانش که به دیواره داخلی قالب نزدیک است به طور مداوم سرد می شود و دانه ها ریزتر هستند. قسمت بالایی به دلیل ایجاد شکاف های هوا و دمای مذاب بالا است که باعث تاخیر در انجماد شمش می شود که سرعت خنک شدن را کاهش می دهد و باعث پسماند انجماد شمش می شود. ساختار کریستالی نسبتاً درشت است، که به ویژه برای شمش های بزرگ آشکار است. با توجه به کاستی های فوق، روش ریخته گری خمشی عمودی با بیلت در حال حاضر در حال توسعه است. یک شرکت آلمانی از یک کاستور پیوسته خمشی عمودی برای آزمایش ریخته گری (16-18) میلی متر × 680 میلی متر نوارهای برنزی قلع مانند DHP و CuSn6 با سرعت 600 میلی متر در دقیقه استفاده کرد.
د. ریخته گری پیوسته رو به بالا
ریخته گری پیوسته رو به بالا یک فناوری ریخته گری است که در 20 تا 30 سال گذشته به سرعت توسعه یافته است و به طور گسترده در تولید بیلت های سیم برای میله های سیم مسی روشن استفاده می شود. از اصل ریخته گری مکش خلاء استفاده می کند و از فناوری توقف کشش برای تحقق ریخته گری مداوم چند سر استفاده می کند. دارای ویژگی های تجهیزات ساده، سرمایه گذاری کم، اتلاف فلزات کمتر و روش های آلودگی محیطی کم است. ریخته گری پیوسته رو به بالا به طور کلی برای تولید بیلت های مس قرمز و سیم مسی بدون اکسیژن مناسب است. دستاورد جدید توسعه یافته در سال های اخیر، محبوبیت و کاربرد آن در لوله های با قطر بزرگ، برنج و کوپرونیکل است. در حال حاضر، یک واحد ریخته گری پیوسته رو به بالا با خروجی سالانه 5000 تن و قطر بیش از Φ100 میلی متر توسعه یافته است. بیلت های سیم سه تایی آلیاژی برنجی معمولی باینری و مس سفید روی ساخته شده اند و بازده بیلت های سیم می تواند به بیش از 90٪ برسد.
E. سایر تکنیک های ریخته گری
فناوری بیلت ریخته گری مداوم در حال توسعه است. این عیوب مانند علائم دال بر روی سطح بیرونی بیلت به دلیل فرآیند توقف کشش ریخته گری پیوسته رو به بالا غلبه می کند و کیفیت سطح عالی است. و به دلیل ویژگی های انجماد تقریبا جهت دار آن، ساختار داخلی یکنواخت تر و خالص تر است، بنابراین عملکرد محصول نیز بهتر است. تکنولوژی تولید بیلت سیم مسی ریخته گری پیوسته نوع تسمه ای در خطوط تولید بزرگ بالای 3 تن کاربرد فراوانی دارد. سطح مقطع دال به طور کلی بیش از 2000 میلی متر مربع است و به دنبال آن یک آسیاب نورد پیوسته با راندمان تولید بالا می باشد.
ریخته گری الکترومغناطیسی در اوایل دهه 1970 در کشور من آزمایش شده است، اما تولید صنعتی محقق نشده است. در سال های اخیر، فناوری ریخته گری الکترومغناطیسی پیشرفت زیادی داشته است. در حال حاضر، شمش مس بدون اکسیژن Φ200 میلی متر با موفقیت با سطح صاف ریخته گری شده است. در عین حال، اثر تکان دهنده میدان الکترومغناطیسی بر روی مذاب می تواند باعث حذف اگزوز و سرباره شود و مس بدون اکسیژن با محتوای اکسیژن کمتر از 0.001٪ به دست آید.
جهت فن آوری جدید ریخته گری آلیاژ مس بهبود ساختار قالب از طریق انجماد جهت دار، انجماد سریع، شکل دهی نیمه جامد، هم زدن الکترومغناطیسی، درمان دگرگونی، کنترل خودکار سطح مایع و سایر ابزارهای فنی با توجه به تئوری انجماد است. ، متراکم کردن، خالص سازی و تحقق عملیات مداوم و شکل دهی نزدیک به پایان.
در درازمدت، ریختهگری مس و آلیاژهای مس، همزیستی فناوری ریختهگری نیمه پیوسته و فناوری ریختهگری پیوسته کامل خواهد بود و نسبت کاربرد فناوری ریختهگری پیوسته همچنان افزایش مییابد.
فناوری نورد سرد
با توجه به مشخصات نوار نورد و فرآیند نورد، نورد سرد به شکوفه، نورد متوسط و نورد نهایی تقسیم می شود. فرآیند نورد سرد نوار ریخته گری با ضخامت 14 تا 16 میلی متر و شمش نورد گرم با ضخامت حدود 5 تا 16 میلی متر تا 2 تا 6 میلی متر را بلومینگ می گویند و روند ادامه کاهش ضخامت به قطعه نورد شده نورد میانی می گویند. ، نورد سرد نهایی برای برآوردن نیازهای محصول نهایی را نورد نهایی می گویند.
فرآیند نورد سرد نیاز به کنترل سیستم کاهش (نرخ پردازش کل، سرعت پردازش عبور و نرخ پردازش محصول نهایی) با توجه به آلیاژهای مختلف، مشخصات نورد و الزامات عملکرد محصول نهایی، انتخاب معقول و تنظیم شکل رول، و انتخاب منطقی روانکاری دارد. روش و روان کننده اندازه گیری و تنظیم تنش
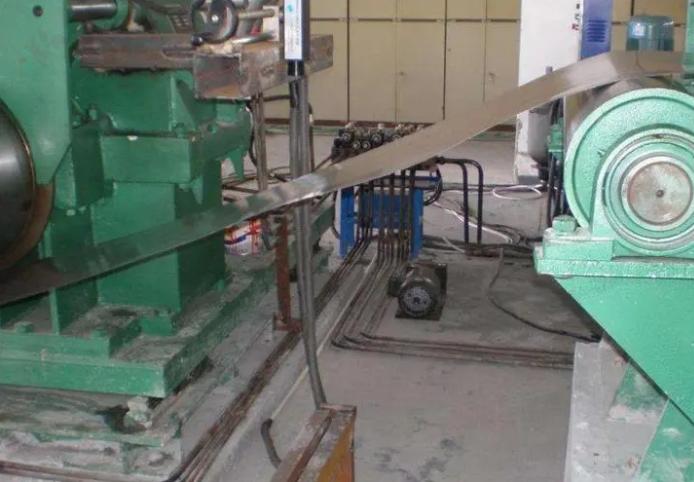
کارخانه های نورد سرد معمولاً از آسیاب های نورد معکوس با چهار ارتفاع یا چند ارتفاع استفاده می کنند. کارخانه های نورد سرد مدرن عموماً از یک سری فناوری مانند خمش غلتک مثبت و منفی هیدرولیک، کنترل خودکار ضخامت، فشار و کشش، حرکت محوری رول ها، خنک سازی قطعه ای رول ها، کنترل خودکار شکل صفحه و تراز خودکار قطعات نورد استفاده می کنند. ، به طوری که می توان دقت نوار را بهبود بخشید. تا 0.005±0.25 میلی متر و در 5I از شکل صفحه.
روند توسعه فناوری نورد سرد در توسعه و کاربرد آسیاب های چند رول با دقت بالا، سرعت نورد بالاتر، کنترل دقیق تر ضخامت نوار و شکل و فن آوری های کمکی مانند خنک کننده، روانکاری، کویلینگ، مرکزیت و نورد سریع منعکس شده است. تغییر دهید. پالایش و غیره
تجهیزات تولید - کوره زنگوله
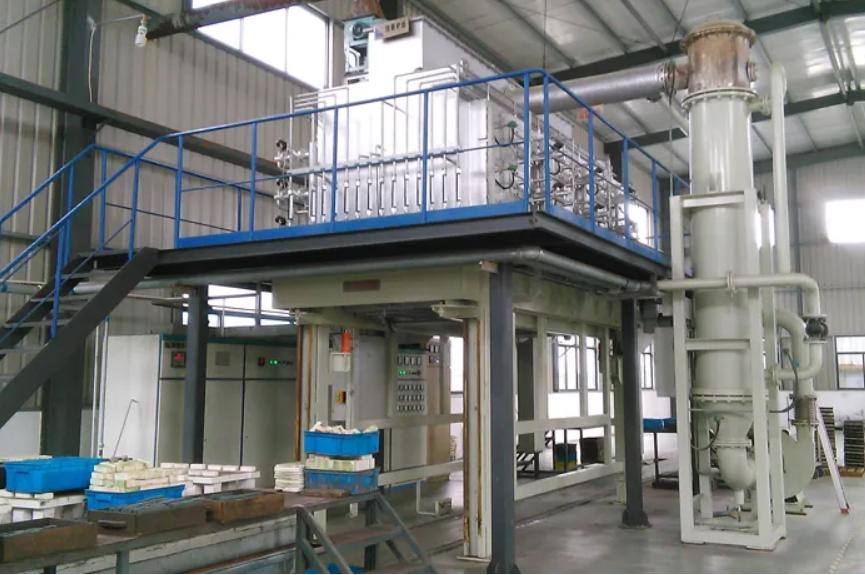
کوره های بل جار و کوره های بالابر عموماً در تولیدات صنعتی و آزمایش های آزمایشی استفاده می شوند. به طور کلی توان زیاد و مصرف برق زیاد است. برای شرکت های صنعتی، مواد کوره کوره بالابر Luoyang Sigma فیبر سرامیکی است که دارای اثر صرفه جویی در انرژی، مصرف انرژی کم و مصرف انرژی کم است. صرفه جویی در برق و زمان، که برای افزایش تولید مفید است.
بیست و پنج سال پیش، برندهای آلمان و فیلیپس، یک شرکت پیشرو در صنعت تولید فریت، به طور مشترک یک دستگاه پخت جدید را توسعه دادند. توسعه این تجهیزات نیازهای ویژه صنعت فریت را برآورده می کند. در طی این فرآیند، کوره زنگ BRANDS به طور مداوم به روز می شود.
وی به نیازهای شرکت های مطرح دنیا مانند فیلیپس، زیمنس، TDK، FDK و ... توجه دارد که از تجهیزات بسیار باکیفیت BRANDS نیز بهره مند هستند.
با توجه به پایداری بالای محصولات تولید شده توسط کوره های زنگ، کوره های زنگ به برترین شرکت ها در صنعت تولید فریت حرفه ای تبدیل شده اند. بیست و پنج سال پیش، اولین کوره ساخته شده توسط BRANDS هنوز هم محصولات با کیفیت بالا برای فیلیپس تولید می کند.
مشخصه اصلی کوره تف جوشی ارائه شده توسط کوره زنگ راندمان بالای آن است. سیستم کنترل هوشمند و سایر تجهیزات آن یک واحد عملکردی کامل را تشکیل می دهند که می تواند به طور کامل نیازهای تقریباً پیشرفته صنعت فریت را برآورده کند.
مشتریان کوره جار بل می توانند هر مشخصات دما/جوی مورد نیاز برای تولید محصولات با کیفیت بالا را برنامه ریزی و ذخیره کنند. علاوه بر این، مشتریان همچنین می توانند هر محصول دیگری را با توجه به نیازهای واقعی به موقع تولید کنند و در نتیجه زمان تحویل کالا را کوتاه و هزینه ها را کاهش دهند. تجهیزات پخت باید قابلیت تنظیم خوبی برای تولید انواع محصولات مختلف داشته باشند تا به طور مداوم با نیازهای بازار سازگار شوند. این بدان معناست که محصولات مربوطه باید با توجه به نیاز هر مشتری تولید شود.
یک تولید کننده خوب فریت می تواند بیش از 1000 آهنربا مختلف را برای رفع نیازهای خاص مشتریان تولید کند. اینها به توانایی تکرار فرآیند تف جوشی با دقت بالا نیاز دارند. سیستم های کوره جار بل به کوره های استاندارد برای همه تولیدکنندگان فریت تبدیل شده اند.
در صنعت فریت، این کوره ها عمدتاً برای مصرف برق کم و فریت با ارزش μ بالا به ویژه در صنعت ارتباطات استفاده می شود. تولید هسته های با کیفیت بدون کوره زنگ غیرممکن است.
کوره زنگوله تنها به چند اپراتور در حین زینترینگ نیاز دارد، بارگیری و تخلیه را می توان در روز کامل کرد و پخت را می توان در شب تکمیل کرد و امکان تراشیدن پیک برق را فراهم می کند که در شرایط کمبود برق امروزی بسیار کاربردی است. کوره های جار بل محصولات باکیفیت تولید می کنند و تمام سرمایه گذاری های اضافی به دلیل محصولات باکیفیت به سرعت جبران می شود. کنترل دما و اتمسفر، طراحی کوره و کنترل جریان هوا در داخل کوره همگی کاملاً یکپارچه هستند تا از گرمایش و سرمایش یکنواخت محصول اطمینان حاصل شود. کنترل اتمسفر کوره در هنگام خنک شدن مستقیماً با دمای کوره مرتبط است و می تواند میزان اکسیژن 0.005٪ یا حتی کمتر را تضمین کند. و اینها چیزهایی است که رقبای ما نمی توانند انجام دهند.
به لطف سیستم ورودی برنامه نویسی الفبایی عددی کامل، فرآیندهای پخت طولانی را می توان به راحتی تکرار کرد، بنابراین کیفیت محصول را تضمین می کند. هنگام فروش یک محصول، بازتابی از کیفیت محصول نیز می باشد.
فناوری عملیات حرارتی
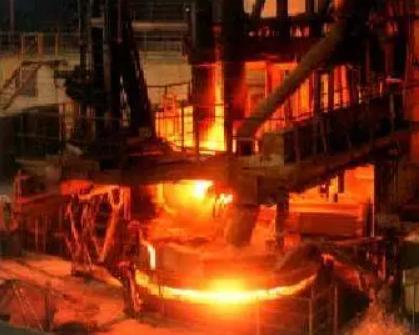
چند شمش آلیاژی (نوارها) با جداسازی شدید دندریت یا تنش ریختهگری، مانند برنز قلع فسفر، نیاز به بازپخت همگنسازی ویژهای دارند که عموماً در کوره جار زنگی انجام میشود. دمای بازپخت همگن به طور کلی بین 600 تا 750 درجه سانتیگراد است.
در حال حاضر، بیشتر بازپخت میانی (بازپخت کریستالیزاسیون مجدد) و بازپخت نهایی (آنیلینگ برای کنترل وضعیت و عملکرد محصول) نوارهای آلیاژ مس با محافظ گاز آنیل روشن می شوند. انواع کورهها عبارتند از: کوره زنگولهای، کوره بالشتکی هوا، کوره کششی عمودی، و غیره. بازپخت اکسیداتیو در حال حذف شدن است.
روند توسعه فناوری عملیات حرارتی در درمان محلول نورد داغ مواد آلیاژی تقویت شده با بارش و متعاقب آن فناوری عملیات حرارتی تغییر شکل، بازپخت روشن مداوم و بازپخت تنشی در یک فضای محافظ منعکس شده است.
Quenching - عملیات حرارتی پیری عمدتاً برای تقویت قابل عملیات حرارتی آلیاژهای مس استفاده می شود. از طریق عملیات حرارتی، محصول ریزساختار خود را تغییر می دهد و خواص ویژه مورد نیاز را به دست می آورد. با توسعه آلیاژهای با استحکام و رسانایی بالا، فرآیند عملیات حرارتی رفع پیری بیشتر اعمال خواهد شد. تجهیزات درمان پیری تقریباً مشابه تجهیزات آنیل است.
فناوری اکستروژن
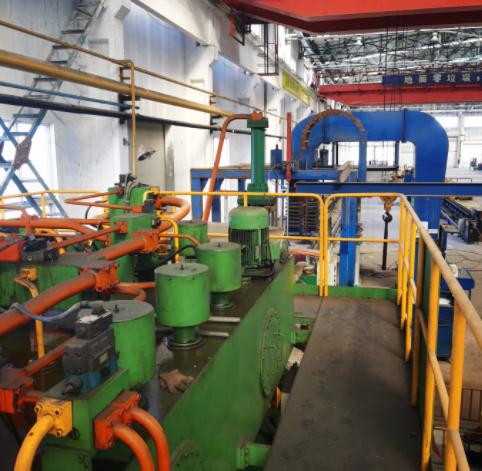
اکستروژن یک روش بالغ و پیشرفته مس و آلیاژ مس، میله، تولید پروفیل و روش تامین بیلت است. با تغییر قالب یا استفاده از روش اکستروژن پرفوراسیون می توان انواع آلیاژهای مختلف و اشکال مختلف سطح مقطع را مستقیماً اکسترود کرد. از طریق اکستروژن، ساختار ریخته گری شمش به یک ساختار پردازش شده تبدیل می شود و بیلت لوله اکسترود شده و بیلت میله دارای دقت ابعادی بالایی هستند و ساختار ریز و یکنواخت است. روش اکستروژن روشی تولیدی است که معمولاً توسط تولیدکنندگان لوله و میله مسی داخلی و خارجی استفاده می شود.
آهنگری آلیاژ مس عمدتاً توسط سازندگان ماشین آلات در کشور من انجام می شود که عمدتاً شامل آهنگری آزاد و آهنگری قالب می شود ، مانند چرخ دنده های بزرگ ، چرخ دنده های حلزونی ، کرم ها ، حلقه های دنده سنکرونایزر خودرو و غیره.
روش اکستروژن را می توان به سه نوع تقسیم کرد: اکستروژن رو به جلو، اکستروژن معکوس و اکستروژن ویژه. از این میان اکستروژن فوروارد کاربرد زیادی دارد، اکستروژن معکوس در تولید میله ها و مفتول های کوچک و متوسط و در تولید خاص از اکستروژن خاص استفاده می شود.
هنگام اکسترود، با توجه به خواص آلیاژ، الزامات فنی محصولات اکسترود شده و ظرفیت و ساختار اکسترودر، نوع، اندازه و ضریب اکستروژن شمش باید به طور معقولی انتخاب شود، به طوری که درجه تغییر شکل نه کمتر از 85٪. دمای اکستروژن و سرعت اکستروژن پارامترهای اساسی فرآیند اکستروژن هستند و محدوده دمای مناسب اکستروژن باید با توجه به نمودار پلاستیسیته و نمودار فاز فلز تعیین شود. برای مس و آلیاژهای مس، دمای اکستروژن معمولاً بین 570 تا 950 درجه سانتیگراد است و دمای اکستروژن از مس حتی به 1000 تا 1050 درجه سانتیگراد می رسد. در مقایسه با دمای گرمایش سیلندر اکستروژن 400 تا 450 درجه سانتیگراد، تفاوت دما بین این دو نسبتاً زیاد است. اگر سرعت اکستروژن خیلی کم باشد دمای سطح شمش خیلی سریع کاهش می یابد و در نتیجه ناهمواری جریان فلز افزایش می یابد که منجر به افزایش بار اکستروژن و حتی ایجاد پدیده خسته کننده می شود. . بنابراین، مس و آلیاژهای مس به طور کلی از اکستروژن با سرعت نسبتا بالا استفاده می کنند، سرعت اکستروژن می تواند به بیش از 50 میلی متر در ثانیه برسد.
هنگامی که مس و آلیاژهای مس اکسترود می شوند، اغلب از اکستروژن لایه بردار برای رفع عیوب سطحی شمش استفاده می شود و ضخامت لایه برداری 1-2 متر است. آب بندی معمولاً در خروجی شمش اکستروژن استفاده می شود، به طوری که محصول می تواند پس از اکستروژن در مخزن آب خنک شود و سطح محصول اکسید نشود و پردازش سرد بعدی بدون ترشی انجام شود. تمایل دارد از یک اکسترودر با تناژ بزرگ با یک دستگاه برداشت همزمان برای اکسترود کردن سیم پیچ یا لوله با وزن بیش از 500 کیلوگرم استفاده کند تا به طور موثری راندمان تولید و بازده جامع توالی بعدی را بهبود بخشد. در حال حاضر، تولید لولههای مس و آلیاژ مس عمدتاً از اکسترودرهای هیدرولیک افقی با سیستم سوراخکاری مستقل (دو عملکرد) و انتقال مستقیم پمپ روغن استفاده میکند و تولید میلگردها عمدتاً از سیستم سوراخسازی غیرمستقل (تک عمل) و انتقال مستقیم پمپ روغن اکسترودر هیدرولیک افقی رو به جلو یا معکوس. مشخصات اکسترودر که معمولاً مورد استفاده قرار می گیرد 8-50 MN است و اکنون تمایل دارد که توسط اکسترودرهای با تناژ بزرگ بالای 40 MN تولید شود تا وزن منفرد شمش افزایش یابد و در نتیجه راندمان تولید و عملکرد بهبود یابد.
اکسترودرهای هیدرولیک افقی مدرن از نظر ساختاری مجهز به قاب یکپارچه پیش تنیده، راهنمای و پشتیبانی بشکه اکستروژن "X"، سیستم سوراخ سازی داخلی، خنک کننده داخلی سوزن سوراخ، مجموعه قالب کشویی یا چرخشی و دستگاه تغییر قالب سریع، پمپ روغن متغیر پرقدرت مستقیم هستند. درایو، شیر منطقی یکپارچه، کنترل PLC و سایر فن آوری های پیشرفته، تجهیزات دارای دقت بالا، ساختار فشرده، عملکرد پایدار، قفل شدن ایمن و کنترل برنامه آسان است. فناوری اکستروژن پیوسته (Conform) در ده سال گذشته پیشرفت هایی داشته است، به ویژه برای تولید میله هایی با شکل خاص مانند سیم های لکوموتیو الکتریکی، که بسیار امیدوارکننده است. در دهه های اخیر، فناوری اکستروژن جدید به سرعت توسعه یافته است و روند توسعه فناوری اکستروژن به شرح زیر است: (1) تجهیزات اکستروژن. نیروی اکستروژن پرس اکستروژن در جهت بیشتری توسعه می یابد و پرس اکستروژن بیش از 30MN به بدنه اصلی تبدیل می شود و اتوماسیون خط تولید پرس اکستروژن به بهبود ادامه می دهد. ماشینهای اکستروژن مدرن کاملاً کنترل برنامه رایانهای و کنترل منطقی قابل برنامهریزی را پذیرفتهاند، به طوری که راندمان تولید تا حد زیادی بهبود مییابد، اپراتورها به طور قابل توجهی کاهش مییابند و حتی امکان عملیات بدون سرنشین خودکار خطوط تولید اکستروژن وجود دارد.
ساختار بدنه اکسترودر نیز به طور مداوم بهبود یافته و کامل شده است. در سالهای اخیر، برخی از اکسترودرهای افقی از یک قاب پیش تنیده برای اطمینان از پایداری ساختار کلی استفاده کردهاند. اکسترودر مدرن روش های اکستروژن رو به جلو و معکوس را درک می کند. اکسترودر مجهز به دو شفت اکستروژن (شفت اکستروژن اصلی و شفت دای) می باشد. در حین اکستروژن، سیلندر اکستروژن با شفت اصلی حرکت می کند. در این زمان، محصول به صورت جهت خروجی مطابق با جهت حرکت محور اصلی و مخالف جهت حرکت نسبی محور قالب است. پایه قالب اکسترودر همچنین از پیکربندی ایستگاه های متعدد استفاده می کند که نه تنها تغییر قالب را تسهیل می کند، بلکه راندمان تولید را نیز بهبود می بخشد. اکسترودرهای مدرن از یک دستگاه کنترل تنظیم انحراف لیزری استفاده می کنند که داده های مؤثری را در مورد وضعیت خط مرکز اکستروژن ارائه می دهد که برای تنظیم به موقع و سریع راحت است. پرس هیدرولیک مستقیم درایو پمپ فشار بالا با استفاده از روغن به عنوان محیط کار کاملاً جایگزین پرس هیدرولیک شده است. ابزارهای اکستروژن نیز با توسعه فناوری اکستروژن به طور مداوم به روز می شوند. سوزن سوراخ کننده خنک کننده داخلی به طور گسترده ای ترویج شده است و سوزن سوراخ کننده و نورد مقطع متغیر تأثیر روانکاری را تا حد زیادی بهبود می بخشد. قالب های سرامیکی و قالب های فولادی آلیاژی با طول عمر بیشتر و کیفیت سطح بالاتر بیشتر مورد استفاده قرار می گیرند.
ابزارهای اکستروژن نیز با توسعه فناوری اکستروژن به طور مداوم به روز می شوند. سوزن سوراخ کننده خنک کننده داخلی به طور گسترده ای ترویج شده است و سوزن سوراخ کننده و نورد مقطع متغیر تأثیر روانکاری را تا حد زیادی بهبود می بخشد. استفاده از قالب های سرامیکی و قالب های فولادی آلیاژی با طول عمر بیشتر و کیفیت سطح بالاتر محبوبیت بیشتری دارد. (2) فرآیند تولید اکستروژن. انواع و مشخصات محصولات اکسترود شده به طور مداوم در حال گسترش است. اکستروژن لولهها، میلهها، پروفیلها و پروفیلهای فوقالعاده با مقطع کوچک و بسیار دقیق، کیفیت ظاهری محصولات را تضمین میکند، عیوب داخلی محصولات را کاهش میدهد، تلفات هندسی را کاهش میدهد و روشهای اکستروژن مانند عملکرد یکنواخت اکسترود را بهبود میبخشد. محصولات تکنولوژی مدرن اکستروژن معکوس نیز به طور گسترده مورد استفاده قرار می گیرد. برای فلزاتی که به راحتی اکسید می شوند، اکستروژن آب بند استفاده می شود که می تواند آلودگی ترشی را کاهش دهد، از دست دادن فلز را کاهش دهد و کیفیت سطح محصولات را بهبود بخشد. برای محصولات اکسترود شده که نیاز به کوئنچ دارند، فقط دمای مناسب را کنترل کنید. روش اکستروژن مهر و موم آب می تواند به هدف دست یابد، به طور موثر چرخه تولید را کوتاه کند و انرژی را ذخیره کند.
با بهبود مستمر ظرفیت اکسترودر و فناوری اکستروژن، فناوری اکستروژن مدرن به تدریج استفاده شده است، مانند اکستروژن همدما، اکستروژن قالب خنک کننده، اکستروژن با سرعت بالا و سایر فناوری های اکستروژن رو به جلو، اکستروژن معکوس، اکستروژن هیدرواستاتیک کاربرد عملی فناوری اکستروژن پیوسته. پرس و انطباق، استفاده از فناوری اکستروژن پودر و اکستروژن کامپوزیت لایه ای مواد ابررسانا با دمای پایین، توسعه روش های جدید مانند اکستروژن فلز نیمه جامد و اکستروژن چند خالی، توسعه قطعات دقیق کوچک، فناوری شکل دهی اکستروژن سرد، و غیره به سرعت توسعه یافته و به طور گسترده توسعه یافته و به کار گرفته شده اند.
طیف سنج
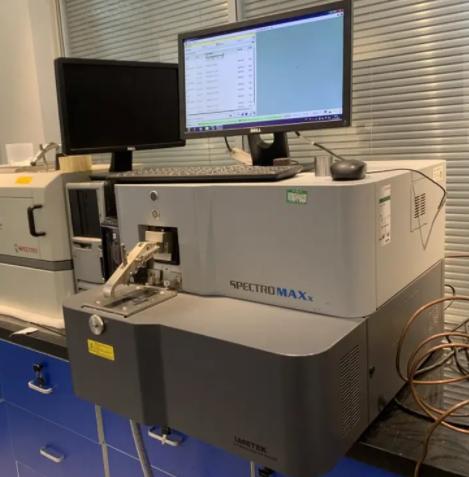
طیف سنجی ابزاری علمی است که نور را با ترکیب پیچیده به خطوط طیفی تجزیه می کند. نور هفت رنگ در نور خورشید بخشی است که با چشم غیرمسلح می توان آن را تشخیص داد (نور مرئی)، اما اگر نور خورشید توسط یک طیف سنج تجزیه شود و بر اساس طول موج مرتب شود، نور مرئی فقط محدوده کمی در طیف را اشغال می کند و بقیه آن هستند. طیف هایی که با چشم غیر مسلح قابل تشخیص نیستند، مانند اشعه مادون قرمز، مایکروویو، اشعه ماوراء بنفش، اشعه ایکس و غیره. اطلاعات نوری توسط طیف سنج گرفته می شود، با یک فیلم عکاسی ساخته می شود، یا با نمایشگر خودکار کامپیوتری نمایش داده می شود و تجزیه و تحلیل می شود. ابزار عددی، تا تشخیص دهد چه عناصری در مقاله موجود است. این فناوری به طور گسترده در تشخیص آلودگی هوا، آلودگی آب، بهداشت مواد غذایی، صنایع فلزی و غیره استفاده می شود.
طیف سنج، همچنین به عنوان طیف سنج شناخته می شود، به طور گسترده ای به عنوان طیف سنج خواندن مستقیم شناخته می شود. دستگاهی که شدت خطوط طیفی در طول موج های مختلف را با آشکارسازهای نوری مانند لوله های مولتی پلایر نور اندازه گیری می کند. این شامل یک شکاف ورودی، یک سیستم پراکنده، یک سیستم تصویربرداری و یک یا چند شکاف خروجی است. تابش الکترومغناطیسی منبع تابش توسط عنصر پراکنده به طول موج یا منطقه طول موج مورد نیاز جدا می شود و شدت آن در طول موج انتخابی (یا اسکن باند معین) اندازه گیری می شود. دو نوع تک رنگ و پلی کروماتور وجود دارد.
تست ابزار رسانایی متر
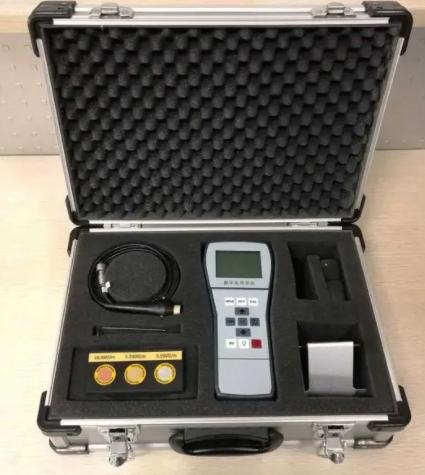
تستر رسانایی فلز دستی دیجیتال (رسانایی سنج) FD-101 از اصل تشخیص جریان گردابی استفاده می کند و به طور ویژه با توجه به الزامات رسانایی صنعت برق طراحی شده است. از نظر عملکرد و دقت استانداردهای تست صنعت فلز را برآورده می کند.
1. رسانایی سنج جریان گردابی FD-101 سه منحصر به فرد دارد:
1) تنها رسانایی سنج چینی که تأیید مؤسسه مواد هوانوردی را گذرانده است.
2) تنها رسانایی متر چینی که می تواند نیازهای شرکت های صنعت هواپیما را برآورده کند.
3) تنها رسانایی سنج چینی صادر شده به بسیاری از کشورها.
2. معرفی عملکرد محصول:
1) محدوده اندازه گیری بزرگ: 6.9٪ IACS-110٪ IACS (4.0MS/m-64MS/m)، که آزمایش رسانایی همه فلزات غیر آهنی را برآورده می کند.
2) کالیبراسیون هوشمند: سریع و دقیق، به طور کامل از خطاهای کالیبراسیون دستی جلوگیری می کند.
3) دستگاه دارای جبران دمای خوبی است: خواندن به طور خودکار تا مقدار 20 درجه سانتیگراد جبران می شود و تصحیح تحت تأثیر خطای انسانی قرار نمی گیرد.
4) ثبات خوب: این نگهبان شخصی شما برای کنترل کیفیت است.
5) نرم افزار هوشمند انسانی: یک رابط تشخیص راحت و عملکردهای پردازش و جمع آوری داده های قدرتمند را برای شما به ارمغان می آورد.
6) عملکرد راحت: محل تولید و آزمایشگاه را می توان در همه جا مورد استفاده قرار داد و مورد توجه اکثر کاربران قرار گرفت.
7) خود جایگزینی پروب ها: هر میزبان می تواند به چندین پروب مجهز شود و کاربران می توانند در هر زمان آنها را تعویض کنند.
8) وضوح عددی: 0.1% IACS (MS/m)
9) رابط اندازه گیری به طور همزمان مقادیر اندازه گیری را در دو واحد %IACS و MS/m نمایش می دهد.
10) عملکرد نگهداری داده های اندازه گیری را دارد.
سختی سنج
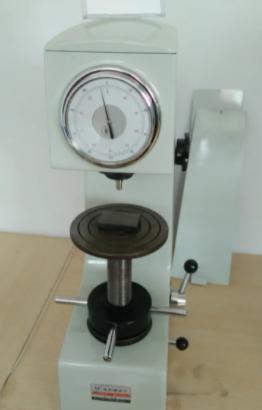
این ابزار یک طراحی منحصر به فرد و دقیق در مکانیک، اپتیک و منبع نور دارد که باعث می شود تصویربرداری تورفتگی واضح تر و اندازه گیری دقیق تر شود. هر دو لنز شیئی 20x و 40x می توانند در اندازه گیری شرکت کنند و دامنه اندازه گیری را بزرگتر و کاربرد را گسترده تر می کند. این دستگاه مجهز به میکروسکوپ اندازه گیری دیجیتال است که می تواند روش تست، نیروی آزمایش، طول فرورفتگی، مقدار سختی، زمان نگهداری نیروی آزمایش، زمان های اندازه گیری و غیره را روی صفحه مایع نمایش دهد و دارای رابط رزوه ای قابل اتصال است. به یک دوربین دیجیتال و یک دوربین CCD. در تولیدات سر داخلی دارای نمایندگی خاصی است.
ابزار تست - آشکارساز مقاومت
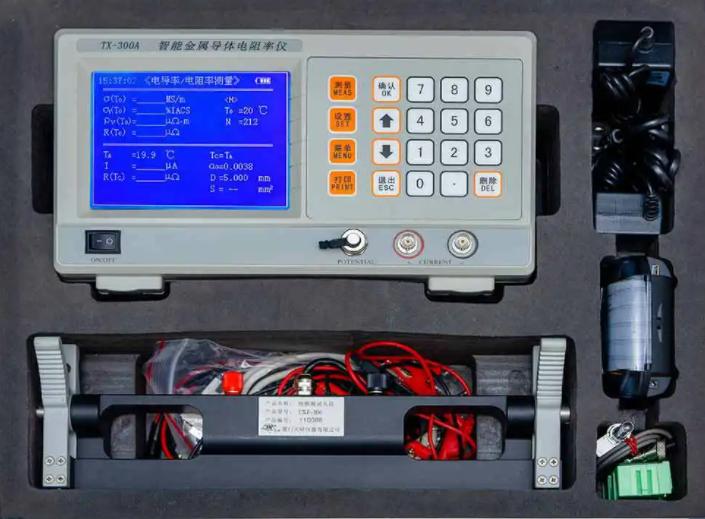
ابزار اندازه گیری مقاومت سیم فلزی یک ابزار تست با کارایی بالا برای پارامترهایی مانند مقاومت سیم، میله و هدایت الکتریکی است. عملکرد آن به طور کامل با الزامات فنی مربوطه در GB/T3048.2 و GB/T3048.4 مطابقت دارد. به طور گسترده در متالورژی، برق، سیم و کابل، لوازم الکتریکی، کالج ها و دانشگاه ها، واحدهای تحقیقاتی علمی و سایر صنایع استفاده می شود.
ویژگی های اصلی ساز:
(1) این فناوری پیشرفته الکترونیکی، فناوری تک تراشه و فناوری تشخیص خودکار، با عملکرد اتوماسیون قوی و عملکرد ساده را ادغام می کند.
(2) فقط یک بار کلید را فشار دهید، تمام مقادیر اندازه گیری شده را می توان بدون هیچ محاسبه ای به دست آورد، مناسب برای تشخیص مداوم، سریع و دقیق.
(3) طراحی با باتری، اندازه کوچک، حمل آسان، مناسب برای استفاده در میدان و میدان.
(4) صفحه نمایش بزرگ، فونت بزرگ، می تواند مقاومت، هدایت، مقاومت و سایر مقادیر اندازه گیری شده و دما، جریان تست، ضریب جبران دما و سایر پارامترهای کمکی را به طور همزمان نمایش دهد، بسیار بصری.
(5) یک دستگاه چند منظوره است، با 3 رابط اندازه گیری، یعنی رابط اندازه گیری مقاومت هادی و رسانایی، رابط اندازه گیری پارامتر جامع کابل، و رابط اندازه گیری مقاومت کابل DC (نوع TX-300B).
(6) هر اندازه گیری دارای عملکردهای انتخاب خودکار جریان ثابت، جابجایی خودکار جریان، تصحیح خودکار نقطه صفر و تصحیح جبران خودکار دما برای اطمینان از صحت هر مقدار اندازه گیری است.
(7) دستگاه تست چهار ترمینال قابل حمل منحصر به فرد برای اندازه گیری سریع مواد مختلف و مشخصات مختلف سیم یا میله مناسب است.
(8) حافظه داخلی داخلی، که می تواند 1000 مجموعه داده اندازه گیری و پارامترهای اندازه گیری را ضبط و ذخیره کند و برای تولید یک گزارش کامل به رایانه بالایی متصل شود.